Sustainability: What brewers are doing
Energy and climate change
We need energy to make our beers. But we are building more energy-efficient brewing systems to lower greenhouse gas emissions and reduce our impact on our climate.
How we use energy
Energy is vital for the brewing sector and is one of the most significant indicators of environmental performance.
There are two main components to total energy use: electrical and thermal energy.
Thermal energy in the form of natural gas is used to generate hot water and steam, which is then used in brewing, packaging and general building heating. It can account for around two-thirds of the total energy consumed but one-third of the total energy cost.
Electrical energy is used to power all the operating brewing equipment (to drive pumps, motors, compressors and fans), non-brewing appliances and internal logistics, with the largest user being refrigeration.
The brewing sector is constantly striving to reduce energy consumption and to move towards using renewable energy to run breweries. Many breweries now obtain 100% of their energy and fuel from renewable sources. The key to cutting the overall energy expenditure is to achieve this goal without sacrificing the quality of the finished product. By improving energy efficiency, both CO2 emissions and the general environmental impact of brewing are reduced.
What we are doing
Breweries across Europe have launched many initiatives to save energy across their beermaking processes.
But before they act, they usually undertake a benchmarking of their energy use to identify areas for improvement. This is one of the most important steps to cutting energy use: start by tracking it. This energy audit helps breweries determine how much energy they are using, how much they are wasting and what kind of measures can be implemented to increase overall operating efficiency in the future.
Here are some of the most effective actions that breweries are doing to cut energy use:
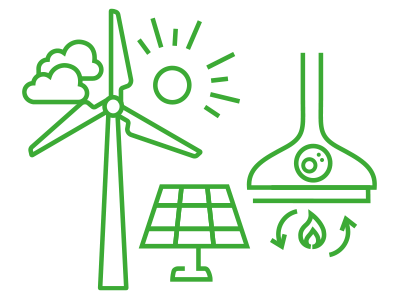
Review boiler and steam systems
Between 25 and 35% of the total energy usage for most breweries can be spent on boiling the wort. Breweries can increase efficiency by better insulating to reduce unwanted heat loss and inspecting equipment for leaks. They can also use heat recovery systems: capturing the heat from the steam produced by boiling, then reusing it for other processes. And ‘wort-stripping’ technologies like a rectifying column can speed up removal of unwanted compounds during wort boiling with reduced energy input. And a flash pasteuriser can cut the heating requirements by around a fifth.
Review refrigeration
Around 35% of the total electrical energy used by most breweries is on refrigeration, but this is easily wasted. Optimising temperature settings by just one degree can produce a reduction of nearly 1-2% in energy usage. Using ammonia as a coolant is much more efficient. And, as with boiling, insulation on piping can further cut waste.
Monitor compressed air
Compressed air systems, which typically consume often around 10% of the total, play a key role in both production and bottling. Brewers should ensure it does not exceed the needed pressures, and that it’s running at optimal efficiency: even a small leak can prove costly over time.
Improve energy efficiency in bottling and packaging
Identifying wastage and making processes more efficient – including only running conveyor systems when needed – can reduce overall energy consumption.
Alternative energy.
Many breweries are using renewable energy sources, like wind, solar and hydrothermal. Others are using biofuels, including some produced on-site, making breweries more self-sustainable while turning otherwise potential waste into valuable secondary products.
Conclusion
The brewing sector has made huge progress in cutting its carbon emissions while improving energy efficiency in the sector. From installing modern, efficient equipment to the reuse of resources to using alternative energy sources, the brewing sector is taking many measures across its production processes to ensure that the entire system uses much less energy – and that the energy it uses is much more efficient.
Energy and climate change: latest initiatives
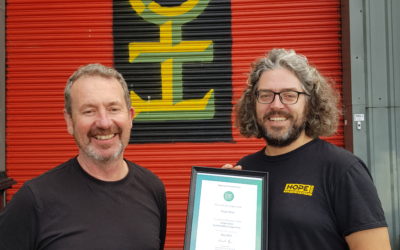
Hope Beers wins Origin Green certification
Irish brewer Hope Beer awarded fourth sustainability prize
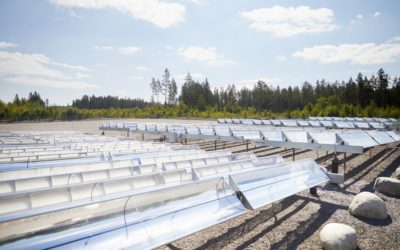
Birra Peroni aims for zero carbon with new solar field installation
Italian brewery Birra Peroni and solar technology company Absolicon are building a new solar field installation to give Peroni solar thermal energy for brewery processes through a heat purchase agreement.
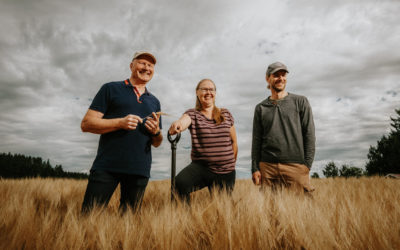
KOFF Christmas Beer uses barley from two regenerative farms
Finland's oldest and most popular Christmas beer, KOFF Jouluolut makes a change for 2022 by sourcing its barley from two regenerative farms
